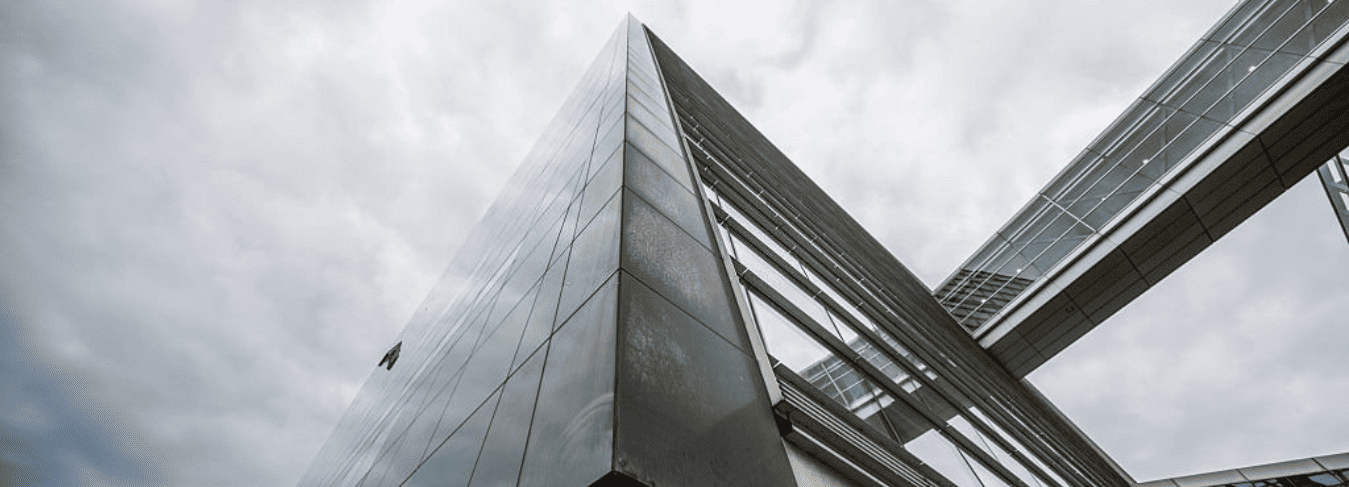
With the gaining popularity of Aluminium Composite Panel in the construction industry, due to their exceptional durability, flexibility, strength, and easy maintenance, it is now ubiquitous facade material. Whether you are a contractor, homeowner, or a facade consultant, understanding the proper ACP installation is important to get successful results. This is why, in this comprehensive guide we will walk you through the process of aluminium composite panel installation.
Gather The Required Tools
Before you start working on the installation process here are a few of the tools you must gather:
- Aluminium Composite Panel from the right manufacturer
- Measuring Tape
- Level
- Electric Saw or Panel Cutter
- Drill
- Screws
- Adhesive tape
- Clamps or Brackets
- Rivets
- Safety equipment (gloves, goggles, etc)
How To Install ACP Sheet?
Step 1: Understand The Location
ACP sheets are available in various thicknesses. For wall cladding, VIVA aluminium composite panel comes in three thicknesses: 3mm, 4mm, and 6mm. While 3mm and 4mm are suitable for both the interior and outside of a building, 6mm is only suitable for a high-rise building's exterior. Only in this way, we can determine the quality of the ACP cladding. This is why while analysing the blueprint, and designing the layout in BIM, make sure you analyse based on the location, whether it is interior or exterior, and how much impact your sheet has to resist, based on these queries you can choose ACP sheets for installation on that basis.Step 2: Measurement

Step 3: Fabrication
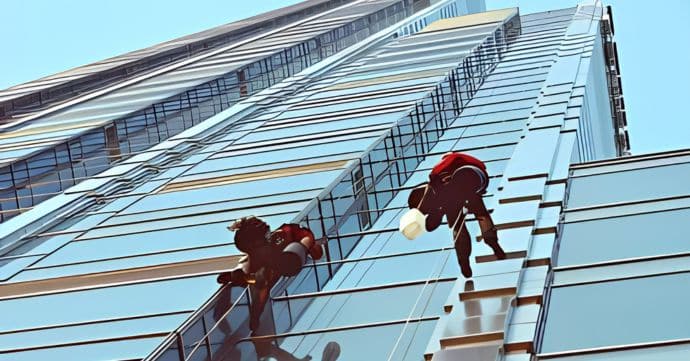
Some necessary equipment required for routing and folding are as follows:
- A manual router with a v-groove blade can be used to process a small number of panels whereas a table circular saw or CNC router is required for large-scale processing.
- Cutting or sawing ACP sheets is a simple procedure that can be accomplished using common commercial metal equipment. Sheet metal punching machines can readily punch Viva ACP panels of any thickness.
- Viva ACP sheet is ideal for shearing since it can be cut with a shear without chipping.
- A three-roll press machine and a press brake machine can readily bend and shape Viva Aluminium Composite Panels. Twist drills normally used for metals and plastics can readily drill Viva ACP material.
- Viva ACPs may be linked together or with other materials using the same rivets that are used in aluminium structures. Aluminium blind rivets with SS (Stainless Steel) screws are recommended for outside usage and high-humidity environments because they prevent corrosion on the edges.
- When using the pasting technique for ACP installation when thermal expansion is predicted, we recommend using only flexible and weather-resistant adhesive. The flexibility of the adhesive should be between 300 and 350%. The adhesive will have a minimum thickness of 3mm and will be conical in form. It is advised to use glue guns while applying glue for ACP cladding installation.
Also Read: ACP Sheet Fabrication/Fitting
Step 4: Waterproofing
Waterproofing is an important part of the ACP panel installation process. Before installing the aluminium composite panels, the weather barrier that will protect the structure must be erected. A primer should be applied to the framings in this phase, and then the barrier should be used to seal the cladding materials.Step 5: Mounting System
Fabricators utilise a mounting technique to guarantee that ACP cladding is straight. The cladding boards are fitted in a predetermined order once the mounting system is applied. The order is determined by a variety of elements, including the importance of shaped sections and corners.Instructions: “ACP Sheet Installation”
To avoid colour differences, the VIVA aluminium composite panel installation must be done in the same direction as the arrow on the protective film; the protective film on the plate must be removed in accordance with the date marked on the protective film to prevent the protective film from ageing and affecting the appearance. We also propose that our clients acquire all of the VIVA’S ACP panels for a comparable project in one order to avoid colour shade differences within a building surface. To prevent damages and scratches on the boards, the customers are advised to use anti-scratch ACP from the house of VIVA.It is also important to consider the safety of workers. While everyone is talking about how to install and maintain ACP sheets safely, VIVA wants to make sure that its fabricators are safe on the site. Using a safety helmet, harness and other necessary equipment during installation are always recommended.
Log on to www.vivaacp.com or call us on our toll-free number 1800 313 3770 for an expert consultation or any specific advice related to the installation of ACP sheets.