Viva's ACP sheets are designed and engineered for easy fabrication, fitting, and installation. Our products are highly tensile and flexible. Proper ACP Fabrication and installation is an important factor in achieving the durability of the panels. The wall panels need the right preparation of the sheets, and the area to be installed, before the installation even begins. The processing of ACP sheets for installation requires numerous tools, and techniques which if exercised in the right way can control and attain a high level of accuracy. The cost of an ACP sheet price with fitting depends on the tools involved, the labour cost of the area, and the time taken to complete the project.
Note : The information provided in this section is just for preliminary reference. We recommend you consult an expert or contact us for specific advice.
Here we have provided you with an insight on how to install Viva ACP sheets.
-
Methodology
-
Edge Bending
-
Methods for Processing
-
Routing And Folding (Tray Formation)
One of the main features of Aluminium Composite Panels is that they can be routed through standard routing machines to internationally designed vertical panel saws, which include hand panel routers with various kinds of routing blades. However, you must keep in mind the choice of routing panel can impact your overall ACP sheet price with fitting. During routing, the floor/base should be flat & free from foreign particles (we recommend using a vacuum cleaner) to avoid denting or bending of ACP sheets. In normal conditions, during routing, the routed sheet plastic thickness should not be more than ½ of one side aluminium skin thickness.
The thickness of the remaining PE/FR core should be uniform throughout the sheet to attain a smooth finish folding or bending. The blade or tip of the routing machine should be appropriate & in good condition for smooth grooving. The distance of the groove from the edge is min 25 mm. After routing cut the corner of the sheet with a sharp blade or wood chisel wider than the corner to find very smooth corner joints. Fold the sheets gently with equal pressure to avoid deflection of the panel, and hump generation & achieving a smooth panel finish. It is suggested to route the sheet from the bottom side only to avoid long-term property problems on coated surfaces. Generally, the reverse bending of the routed area is not allowed.
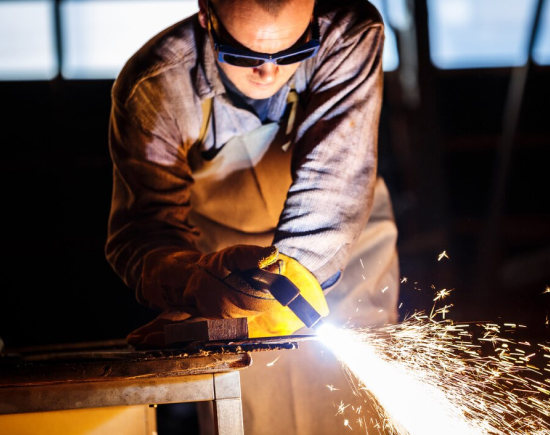
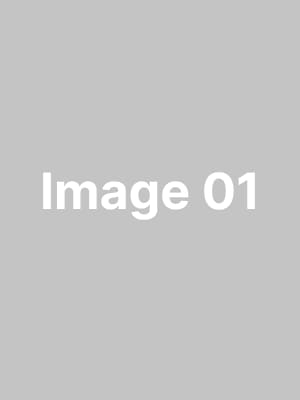
Equipment used for Routing & Folding
For processing a small number of panels a manual router with a v-groove blade can be used. For processing large numbers a table circular saw or CNC router is needed.
The manual router consists of circular grooving blades that are commonly available on the market and are used for manual processing. If they are equipped with special routing bits (carbide tipped cutter) the hand-operated router can be used for a limited number of processes. In this case, the stability of the tool and the guide system considerably affect the quality of the routing, the setting of the manual router is very important, it is highly dependent on operator skills. The router rpm should be 2400 to 5000 & Router wheel dimensions is D4”x90°xB20mmxT-10mmx6T or D4”x90°xB20mmxT-12mmx6T.
These types of routers consist of a moving arm with a circular blade/bit. Fix the sheet on a vertical supporting plate, and set the grooving depth by setting the wheel. The plate should be flat and free from dents to find uniform routing.
This machine consists of a computer along with programming and an automatic robotic arm. Set the depth & design of routing, and then select the appropriate bit for the routing angle. Manual routers are more economical than automatic tools, however, the manual router can be used for a limited number of processes, but with the automatic router, you can get multiple routed panels by setting the program in one go. This creates a difference in ACP sheet price with fitting in terms of labour involved and time consumed to get the same work done.
Cutting / Sawing of ACP Sheet
Sawing or cutting of ACP sheets is an easy process that can be done with ordinary commercial metal equipment. Saw blades and router bits are available at independent distributors who handle cutting tools. Before processing large quantities, the trial saw cuttings should be done to evaluate both the tool working conditions and the recommended cutting speeds of 3000 to 5000 rpm. For marking the panels the use of a soft pencil us adequate. High-speed bands and circular saws with cutting speeds of up to 30 m/min are recommended. Depending on the thickness of the Aluminium Composite Panel, saw blades with a 5 to 10 mm tooth pitch should be used. For circular saws, a tooth geometry with alternating flat/trapeze teeth and carbide tips is normally recommended to ensure that edges are free of burrs. Adjust the saw blade diameter (O) and number of teeth for the material to be processed as well as the type of saw and its speed. To ensure clean cutting edges without any chips, the panel material should always be clamped to ensure that it is vibration-free.
This particularly applies to Aluminium Composite panels of 3 to 6 mm thicknesses. When using jigsaws, make sure the saw blades are sharp and are not straight-set (plastic, PVC). Manual feeding must be carried out slowly and evenly.
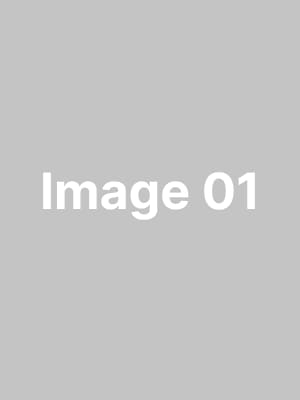
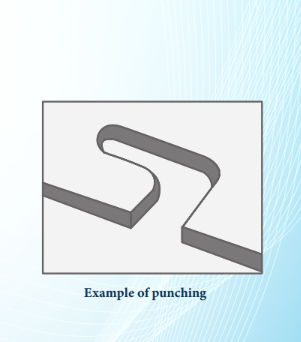
Punching
Viva ACP Panel of any thickness can be punched easily using sheet metal punching machines. For burr-free cuts use sharp tools & dies with a minimum cutting clearance of 0.10 mm. For punching & shearing strength please refer to our grade-wise technical data sheets. The distance from one hole to another hole will be 5 mm & minimum diameter of the punch should be 5mm also.
During punching sheet may be deflected, so re-straitening may be required. Do not remove the protective film before the completion of the process.
-
Perforated sheet (Multiple Punched)
-
Single Punch
Shearing
Viva ACP is highly suitable for cutting with shear without any chipping. The gap between the upper & lower shear will be 0.1mm & angle 1° to 5°.
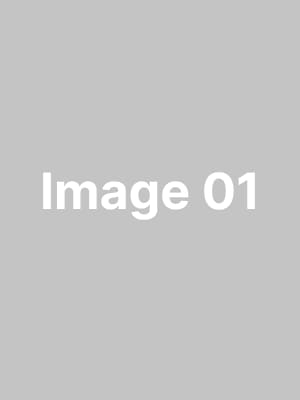
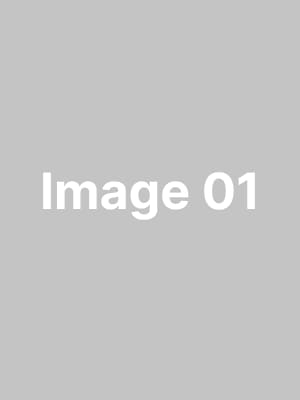
Drilling
Viva ACP is highly suitable for cutting with shear without any chipping. The gap between the upper & lower shear will be 0.1mm & angle 1° to 5°.
-
A. Three Roll System Press Machine :
Viva Aluminium Composite Panels can easily be bent and shaped by three roll press machines & press brake machines :
-
B. Press Brake Method
When bending or forming with a press brake, use a top die with the radius desired for bending and open the bottom die (jaws) approximately two times the thickness of the material plus film wider than the top die. The lower die should always have a protective pad which should not be less than 2mm. Some adjustment of the lower jaws is necessary to allow for varying bending properties. The radius of the top die will be the approximate inside radius of the finished panel.
Bending
Viva ACP material can be easily drilled with twist drills commonly used for metals & plastics.
The twist drill will be high-speed steel with a tip angle of 100° to 140°.
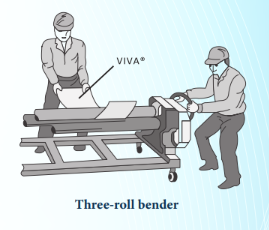
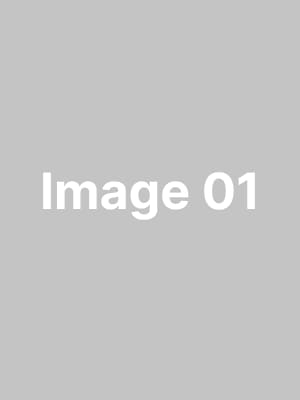
Counter Sinking
A hole is to cut a conical hole into a Sheet/metal object. This process is normally used to create space for the head of a screw or bolt to sit flush with the surface of the material or to clean away burrs left from drilling and tapping. Counter sinking screw is allowed only for interior use.
Riveting
Viva ACPs can be fastened together or joined with other materials with rivets common to aluminium constructions. For exterior use & high humidity areas, it is suggested to use aluminium blind rivets with SS (Stainless Steel) screw which prevents corrosion on edges.
-
The shaft diameter of the blind rivet should be 5 to 6 mm and the head diameter is 10 to 15 mm.
-
Please take the thermal expansion of the panel into account e 2.4mm/m/100 C to avoid deflection of a panel the hole in the panel should be large enough to allow the expected according to sheet length.
-
The Rivet head should cover a minimum of 1.5mm surrounding area.
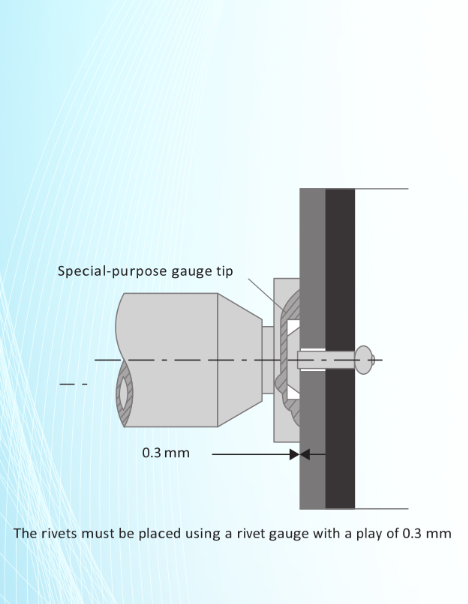
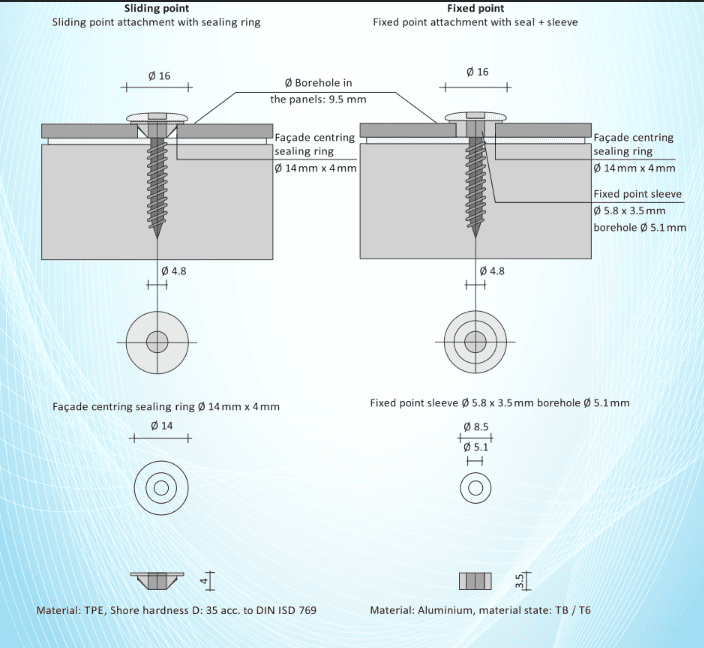
Screwing
Viva ACPs can be fastened together or joined with other materials with rivets common to aluminium constructions. For exterior use & high humidity areas, it is suggested to use aluminium blind rivets with SS (Stainless Steel) screw which prevents corrosion on edges.
Pasting
Where ACP sheets are installed with the pasting method and thermal expansion is expected, we recommend using flexible & weather resistance glue only. The flexibility of glue should be approximately 300-350%. The glue thickness will generally be a minimum of 3mm and will be in a conical shape. The glue will be applied with glue guns. If the spacer is required then the glue height will be 2 times of spacer height. The double-headed tape can also be of the same thickness. Please also follow the instructions of the glue or tape supplier. The surface should be free from foreign particles, contamination of chemicals & water.
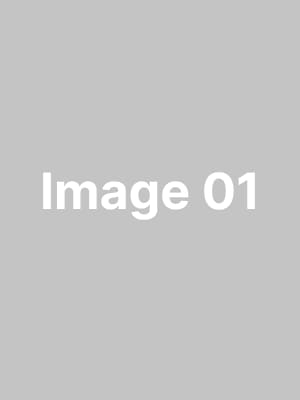
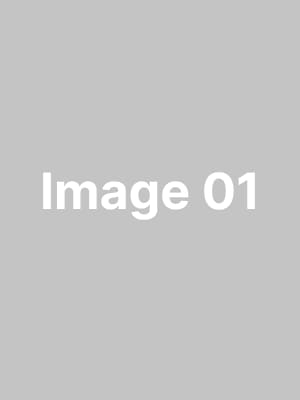
Tray Installation
Viva ACP can be easily used by making a tray; the following instructions should be taken for ACP installation.
-
Panels should be fabricated into the tray with an aluminium frame.
-
All joints should be protected with an approved sealant.
-
The finished tray should be delivered to the site complete with component marking for easy identification and assembly.
-
Fasteners including screws, nuts, bolts, and other items required for joining the panel should be non-magnetic stainless steel.
-
Rivets used for fastening the frames should be of aluminium, large flange head type with stainless steel mandrel.
-
All other fixing materials should be of aluminium or stainless steel.
-
Defective panels having warped, bowed, dents, scratches and broken must not be installed.
-
Supporting brackets should be designed to provide three-dimensional adjustments and accurate location of wall components.
-
All joints should be of specified widths. No two adjacent or perpendicular joints should have a difference in width of more than 2.5 mm. Tolerance between adjacent panels across any joints should not exceed 1.5 mm locally.
Follow these tips to slay your routing and fabrication process of VIVA's ACP sheets
Below is a quick reference guide for the thermal resistance of VIVA's aluminium composite panel
Temperature Resistance - 50ºC ~ +80ºC | Linear Expansion 2.4mm per meter at 100ºC
Keep in mind that the coating integrity will be compromised if the working temperature approaches or exceeds 100ºC.