Triple the Brilliance with Viva- India's Sole Triple Coating Innovator
An Overview of Pre-Painted Aluminum Coil Production
-
Pre-Painted Aluminum Coil Production Capacity : 24,000 MT / Per Year
-
Having Facility to customize the shade either Solid Metallic or any Pattern.
-
Using High accuracy technology to meet the client requirements.
-
Fully Equipped laboratory to commit the life of the product and perform the real time testing.
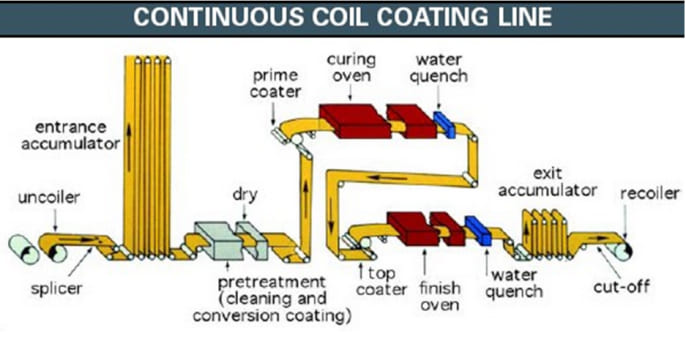
Viva Creating The Premium Pre-Painted Aluminum World
At Viva, we endeavor to make your yearning Product dreams into a reality. We define ourselves as one of the leading manufacturers and suppliers of high-quality Pre-Painted Aluminium Coil in India. Our journey started with a humble beginning long back in 2003 at Mumbai in Maharashtra and over the years the value we have contributed to the industries is synonymous with Trust and Reliability.
Viva had set up its 1st coating line in 2018. With the single coat and single baked with the thin gauge capacity. Min. Thickness we have facility to coat on this machine is 0.05mm with very fine precision.
To meet the market demands Viva had installed 2nd coating line in 2020. Which is also a unique technology i.e. 3 coat two backed with printing facility. And it meet the market requirment from 0.10mm to 2mm.
-
Again, based on the market boost Viva installed 3rd coating line. Which is 3 Coat and 3 Bake system. It is a unique technology which is available 1st time in India in PPAL market.
-
Based on all the above 3 continues coating line Viva has a huge capacity and specifications to feed into the market.
-
Viva also having Embossed finish available in PPAL.
-
Now Days Viva is making the benchmarking for the available coating system and available finishes with the best quality.
-
Viva is working with very premium customers for the premium market. Which need precise coating technology.
-
Viva having the testing facility to meet the ECCA And ASTM Standards.
-
Viva equipped with the reputed equipment suppliers.
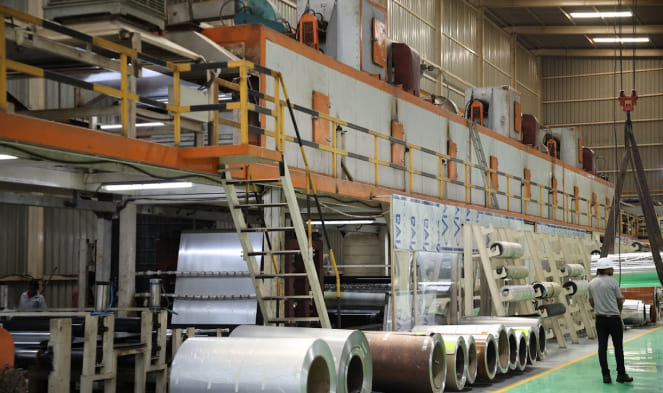
Technologies Incorporated
Coil Coating Line Process
Testing Facilities
01
- Standard: ASTM D1200
- Tests: Viscosity (BS3900) @30°C
02
- Standard: ASTM D1210
- Tests: Fine-ness Of Grinding
03
- Standard: ASTM D1475
- Tests: Specific Gravity @ 30°C
04
- Standard: ASTM D1353
- Tests: % Of Non-Volatile Material (NVM%)
05
- Standard: ASTM D1400
- Tests: DFT (µ)
06
- Standard: ASTM D523
- Tests: Gloss @ 60°GH
07
- Standard: ASTM D2244
- Tests: Colour Measurement
08
- Standard: ASTM D2794
- Tests: Reverse Impact
09
- Standard: ECCA - T6
- Tests: Cupping
10
- Standard: ASTM D4145
- Tests: T-Bend
11
- Standard: ASTM D5402
- Tests: MEK Double Rubs
12
- Standard: Pencil Hardness
- Tests: ASTM D3363
13
- Standard: BS3900 E2
- Tests: Scratch hardness (Kg)
14
- Standard: ASTM D4060
- Tests: Abrasion Resistance (Taber Abraser)
15
- Standard: ASTM D3359
- Tests: Dry Adhesion Test (Cross Test)
16
- Standard: AAMA 2605
- Tests: Wet Adhesion Test (Water Boiling)
17
- Standard: ASTM B117
- Tests: Salt Spray Test (Corrosion Resistant)
18
- Standard: ASTM D1308
- Tests: Chemical Resistance (HCl)
19
- Standard: ASTM D1308
- Tests: Chemical Resistance (NaOH)
20
- Standard: ASTM G154
- Tests: Gloss Retention by UV M/C
21
- Standard: ASTM G154
- Tests: Chalk Resistance by UV M/C
22
- Standard: ASTM G154
- Tests: Colour Deviation by UV M/C
23
- Standard: ASTM D2247
- Tests: Humidity Test
PPAL Coil Coating Available
Application Area
Aluminum Coating Line Specifications
Details | Line - 1 | Line - 2 | Line - 3 |
---|---|---|---|
Thickness (mm) | 0.05mm - 0.4mm | 0.15mm to 3mm | 0.15 mm to 1.5 mm |
Width (mm) | Min. 575 & Max. 1250 | Min. 575 & Max 1650 | Min. 575 & Max 1650 |
Coil ID (mm) | 150 / 405 / 508 | 405 / 508 | 405 / 508 |
Coil ID (mm) | 1800 | 1800 | 1800 |
Coil Weight (Kg) | 1000 to 3000 | 1000 to 3500 | 1000 to 3500 |
Other Specification
Alloy Grade | 3003/3004/3005/3105/1050/5052/5754/5005 etc |
---|---|
Tamper | H42 / H44 / H46 / H48 |
Specification | ASTM-B-209 , AAMA-2605, EN 485, EN 573, EN 1396, DIN 1745 , DIN 1783, BS 1470 |
Coating Standards | ECCA / ASTM / EN / AAMA |
ISO Standards | ISO 9001:2015, ISO 14001:2015 & ISO 45001:2018 |
Pre-Treatment Type | Tetravalent Chrome / Chrome Free (ROHS) |
Packing | Eye To Wall / Eye to Sky On Wooden Pallet Corrugated wrapper with foam Support and stretch wrapped |
Packed Coil Weight (Kg) | 1000 - 3000Kg |
Pellet Max Height | 1.3 meter |
FAQ'S
Color coated aluminum coils are aluminum sheets coated with layers of protective and decorative paint, offering durability and vibrant finishes for various applications like roofing, facades, and signage.
They provide excellent corrosion resistance, lightweight durability, and aesthetic appeal, making them ideal for architectural and industrial uses.
Common coatings include PVDF (Polyvinylidene Fluoride) for superior weather resistance and PE (Polyester) for vibrant colors and flexibility.
Thickness options typically range from 0.1mm to 1.2mm, catering to diverse project requirements.
PE coatings offer flexibility and vibrant colors, suitable for interiors, while PVDF coatings ensure high durability and weather resistance for exterior applications.
The coils are cleaned, pretreated, and layered with paint through continuous coil coating, ensuring uniform adhesion and long-lasting finishes.