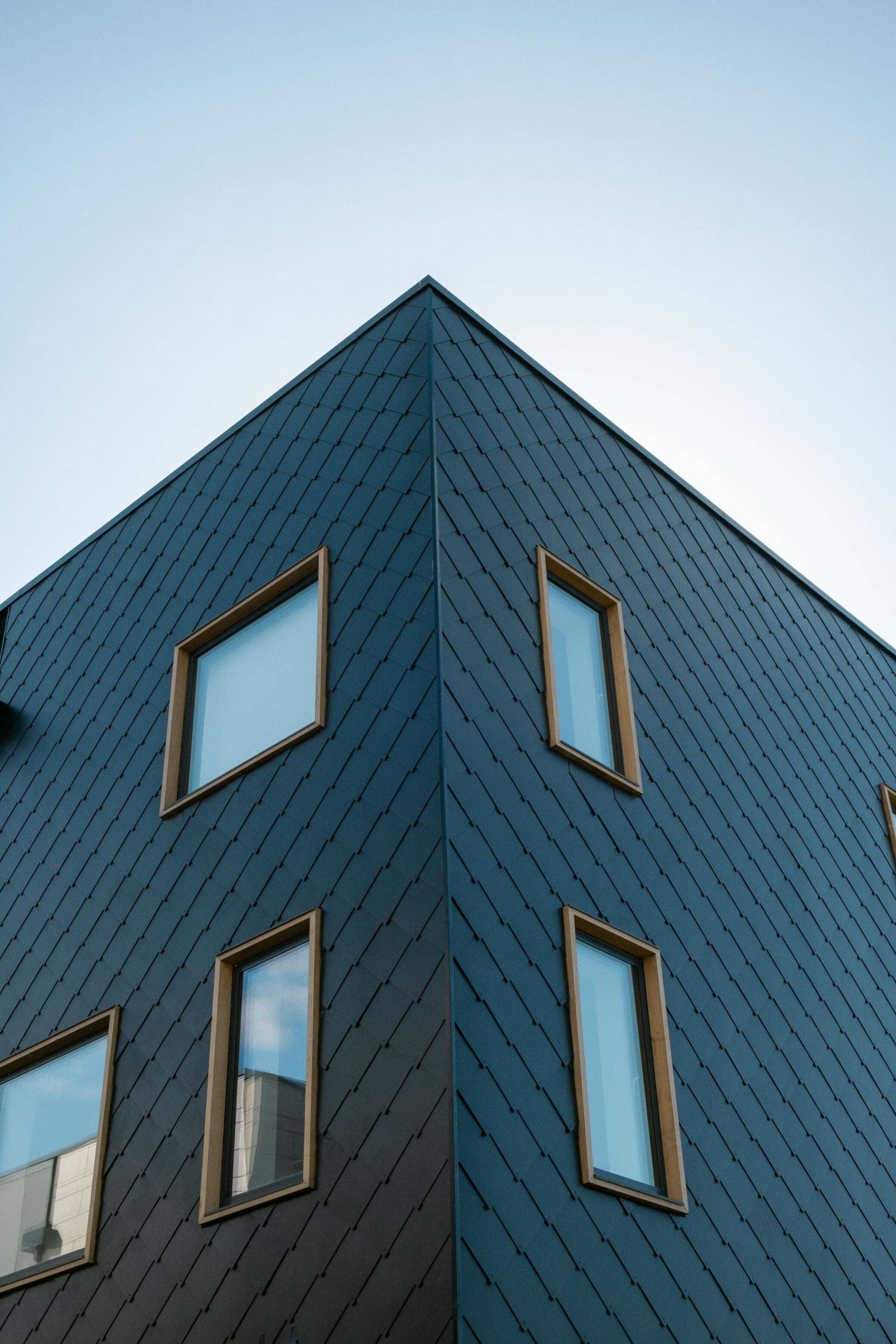
Facilities
One of the rare Indian ACP manufacturers to be equipped with a dedicated in-house R&D unit
At Viva, we stand by the fact that technology is something that can make a massive contribution to the quality of production. This is the reason why our business strategy and our team continuously strives to improve the manufacturing technologies and successfully introduce new products. Known for its most stringent ISO certificates, TUV-SUD team applauded Viva for all its manufacturing processes. Viva has more than 100+ in house equipment to test its products.
Technological development and improvement in manufacturing processes have been the foundation of the Viva since its inception. It makes us immensely proud as we are one of the few ACP sheet manufacturers in India with in-house R&D facilities.
At Viva, our research and development strategies are always aimed towards achieving perfection in whatever we do and staying ahead of rapidly increasing marketing demand for top-notch quality ACP Panels. Our team has specialized knowledge and expertise to manufacture first-class ACP Claddings.
Why Us?
Promises Made. Promises Kept.
UNMATCHED TEAM
It is needless to mention the fact that it is the team of a company that ultimately determines its success or failure. They are the primary reason we have been able to boost our sales and revenue and successfully function by delivering superior quality Aluminium Composite Sheets all across the country.
REMARKABLE MANUFACTURING PROCESSES
Our manufacturing processes are backed by continuous research and development as it provides us with valuable knowledge and insights, leads to improvement in existing ACP sheet manufacturing processes, and determines where efficiency can be boosted and costs can be reduced. Our multiple awards and certificates by numerous certification authorities are the result of our unique manufacturing processes.
CONTINUOUS INTEGRATION
We have successfully achieved absolute perfection in the quality of our Aluminium Composite Panels, be it the design, shade, colour or quality of production. Our unique manufacturing system and continuous integration processes help us to develop innovations that strengthen the company’s position in the vast marketplace.
Laboratory
In-house laboratory Testing Facility
Ash Content
An in-house lab engineer and supervisor should measure the ash content in FR thermoplastic granules by making use of the Desiccator, Tong, and crucible.
Impact Tester
A test of the coating's ability to resist cracking and peeling will require dropping loads from different heights
Pencil Hardness
To determine the resistance of the painted layer or metal surface against the hardness of the pencil by holding the same at 45° and adding a load of 250 gm on the holder.
Tensile Strength
To examine the tensile strength of raw materials, plastic core, and finished goods by the QC Engineer or the Lab Supervisor.
Chemical Test
To investigate whether home chemicals cause any objectionable effects on clear and pigmented organic surfaces, such as discoloration, gloss change, blistering, softening, swelling, loss of adhesion, etc.
Melt Flow Index
To determine the melt flow rate of the molten thermoplastic resin using MFI Machine, Die, Piston, Weighing Balance, and Weight (2.16 & 4.9kgs)
QUV Testing
It is performed to test the long term property of coated surface like gloss retention, colour retention and chalking rating of surfaces.
Color Matching Cabinet
Color matching and determining metamerism of color between two master specimens under different lighting, e.i. Light D65, TL84, UV, CWF, TFL.
Cross Hatch
To evaluate the wet and dry adhesion of paint on the coated surface of the base metal by manually counting the number of peeled squares and rate the adhesion from 5B to 0B.
Moisture Analyzer
To determine the moisture/ water content in granule and other solid content using hot air circulating oven, tong, Petri dish, desiccators, and analytical weighing balance.
Specific Gravity
To determine the density of granules with the aid of a Micro weighing balance, N-Butyl Acetate, Glass Beaker, and a balance accessory.
Coating Adhesion
Used to check the bonding strength (adhesion) between paint and aluminium or bonding strength between multiple layers of paint. Tests like hot water boiling, cross hatch, tape off methods are involved.
Elongation
To examine the tensile strength of raw materials, plastic core, and finished goods by the QC Engineer or the Lab Supervisor.
Peel Off Strength
To determine the adhesive Bonding Strength of finished good materials with the aluminum sheet
Specular Gloss
To check the reflectance value (Gloss level) on the coated surface.
Boiling Water Resistant
To visually observe for signs of delamination, blisters, shrinkage, or water penetration under the coated surface on exposure to boiling water.
Dry Film Thickness
These 3 coat finishes will typically consist of a 5-7 micron primer coat, 18-20 micron color coat and a 5 -7 micron clear coat for a nominal dry film thickness of 35(+/-)2 micron.
Salt Water Testing
Used to check the corrosion resistance of ACM, by a salt spray testing machine also known as SST machine.