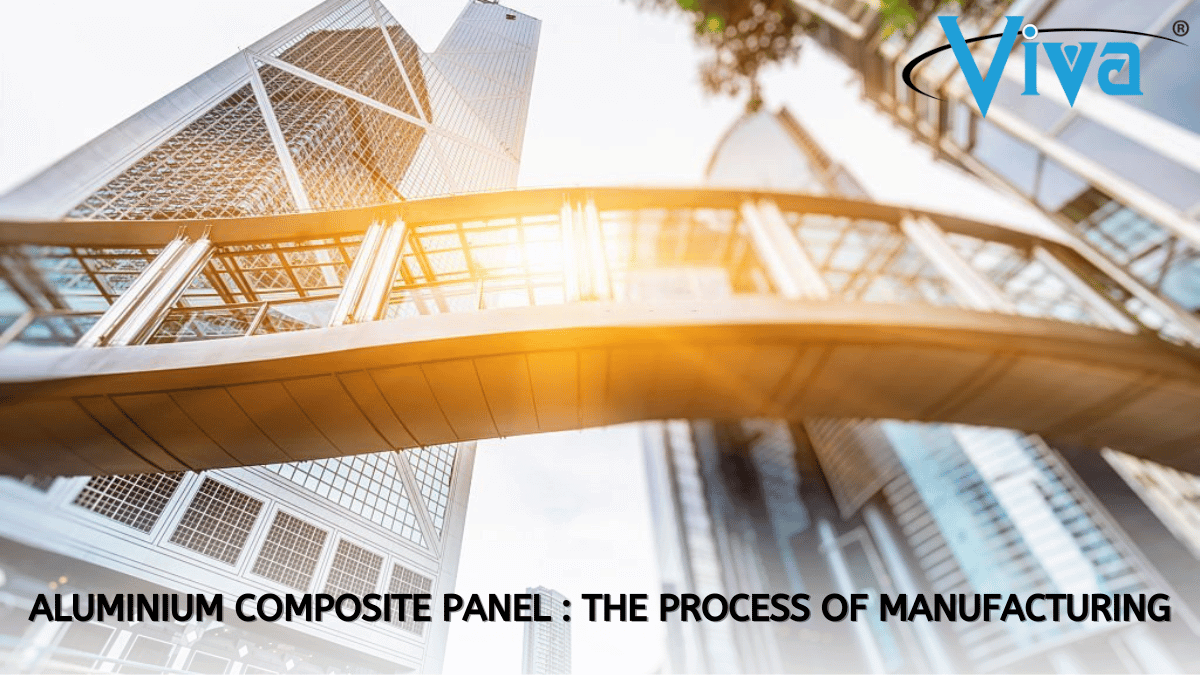
Aluminium composite panels may be made in a variety of ways. Cold composite technique and heat composite method are two types of composite methods for plastic core panels and two-sided aluminium panels, respectively. However, we will discuss how VIVA manufacture their ACP sheets while maintaining the quality standard.
Steps Of Manufacturing Aluminium Panel Sheet
Cleaning
Cleaning the aluminium coil is the first step in the fabrication of composite aluminium sheet. VIVA procure the aluminium coil from Hindalco. As the process of production of demands, the surface of aluminium coils is covered with lubricants and anti-oxidants, and some dirt will adhere during transit, affecting adhesion and necessitating cleaning. We degrease, de-oxidize, and chromatize the coil while passing it through a series of tanks.
Degreasing
Degreasing is a technique for removing oil and other impurities from a surface. To remove the water from the coil, deoxidizing is done, and chromatization is used to create the abrasive surface. For good primer adhesion on aluminium surfaces, an abrasive surface is essential.
Addition of Protective Layer
A dense chemical protective layer forms on the surface of the aluminium coil after cleaning and chemical treatment; this chemical film can increase the aluminium coil's oxidation resistance and extend the life of the paint film. The grains are then melted into sheet shape to create the core. On both sides of the Core, the adhesive (Adhesive sheet is purchased from DuPont) film is applied.
PVDF/FEVE Coating
We at VIVA fed the cleaned aluminium coil to a coater and coat the outside surface of the aluminium coil with a high-performance fluorocarbon resin. Two coats of paint and primer are applied to the panels of the aluminium composite sheet. We use paints that are procured from renowned manufacturers like Nippon, Spectrum, PPG, Monopol, Akzonobel and the customization of shades been manufactured In-house. The topcoat is a fluorocarbon resin coating called polyvinylidene fluoride(PVDF), which is highly weather resistant. Its strong UV resistance and resistance to contamination keep the coated aluminium coil's surface looking attractive. Fluorocarbon coatings are typically applied to aluminium coils using a roll coating process and then dried at high temperatures. There are three layers of paint and to dry each paint coat it must be baked at 240 °C for around 45 seconds.
Adding Top and Bottom Layer
To make a sandwich panel, coils are put on top and bottom of the core. Laminate aluminium coil to the core using induction roller heating. Our ACP has been brought to normal temperature using a cooling tower, and it is now ready to use. The protective film can now be applied to the ACP sheet. The self-adhesive protection film can be removed after installation. To avoid damaging the surface coating during future processing, transportation, and installation, a protective layer is added to the coating's surface. The protective film also comes with the direction of the installation of ACP sheets while ACP cladding.
Customizing Into Right Size
Finally, the ACP board and ACP sheets are cut into the customized length. However, Pallet Packaging is also used by VIVA to preserve sheets during shipping. Loading the sheets into trucks while making sure the ACP reaches the retailer, architects, and facade consultants. Throughout the transportation process, we maintain a consistent communication process.
Voila! Now, it’s time to install the ACP sheets to beautify your façade with VIVA ACP sheets.
Since the process includes technicality, you are requested to call our In-House ACP experts for better clarification. Call us on our toll-free number 1800 313 3770 or write us at info@vivaacp.com.