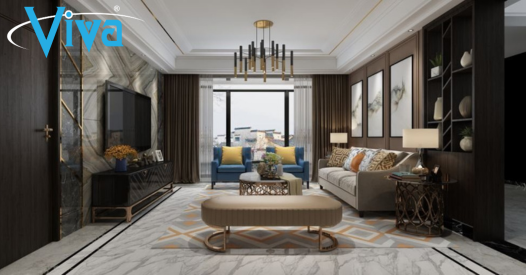
A popular construction material of modern times, ACPs are a well-known name in the industry. Lauded for their low weight and sturdy design, the manufacturing process of these ‘sandwich-like’ materials is quite interesting. Eager to know what the process of making an Aluminium Composite Panel looks like? We have broken it down for you to understand.
A new-age material, ACPs are widely used as cladding, facades, front elevation, signage, and several other applications. Did wonderfully designed building exteriors ever catch your attention? Well, it’s most likely they are clad in ACP panels. At Viva, we have supplied ACPs to numerous projects across India and in several other countries.
Viva’s Manufacturing Facility at Umbergaon, Gujarat
Before we start, let’s take a look at what ACP is made of as well as what our facility looks like. ACP gets its name from Aluminium and Composite materials. Using the latest Korean technology in our state-of-the-art facility located in Umbergaon, Gujarat, we offer the best-in-class panels for exterior and interior usage. We are also one of the few ACP manufacturers in India who are equipped with an internal R&D facility that drives innovation to cater to superior-quality products.
Coming to the composition, Viva ACP panels are bonded to a core material, which is available in different options including polyethylene or mineral-filled core, as well as aluminium corrugated, which are fire-retardant panels.
Pre-treatment of Aluminium Sheets
At Viva, we prioritise the procurement of high-quality raw materials in making our Composite Aluminium Sheets. We take the required steps to clean the sourced aluminium coils from Hindalco.
Hence, the first step in the ACP production process is the pre-treatment of the aluminium sheets. We ensure that the aluminium sheets are thoroughly cleaned and degreased to remove any lubricant, dirt, oil, or other contaminants that may be present. This is an extremely crucial step since this ensures proper adhesion of the coating (following step) to the aluminium sheets.
Coating of the Aluminium Sheets
Once the aluminium sheets have been pre-treated, we use advanced technology to coat them with a layer of paint or lacquer. From protection against corrosion, weather resistance, and aesthetics, the coating provides several functions in the manufacturing of Aluminium Composite Panels.
The coating process involves applying a layer of paint or lacquer to the aluminium sheets. Generally, there are several methods of applying coatings, including coil coating, spray coating, or powder coating. In coil coating, the aluminium sheets are coated while they are still in coil form. In spray coating, the use of a spray gun is used to apply a layer(s) to the sheets, while powder coating uses a dry powder that is electrostatically charged and then sprayed onto the sheets.
After the coating is applied, the sheets are baked at a high temperature to cure the paint or lacquer. This ensures that the coating is fully bonded to the aluminium sheets and provides the desired level of protection and durability.
Bonding of Aluminium Sheets to the Core Material
As the sheets are coated, granules are melted to form the core material. Next, an adhesive film is applied on both sides of the core to make the aluminium sheets stick. The process involves applying a layer of adhesive film that we procure from DuPont Paints to the back of the coated aluminium sheets, which are then pressed against the core using a high-pressure roller.
The strong Aluminium Composite Panels are made when these sheets go through induction roller heating, which applies uniform pressure and heat to them. This helps to ensure that the adhesive is evenly distributed and fully bonded to the aluminium sheets and core material. Viva offers several variations in the core material such as LDPE, mineral-filled, fire-retardant, and aluminium corrugated. Next, the sheets enter the cooling tower, which brings them down to an average temperature.
Application of the PVDF/FEVE Coating
Viva takes pride in claiming that the ACP panels we produce are long-lasting and resistant to weathering and corrosion. This is because our panels get coated with protective coatings, out of which the topmost coat is polyvinylidene fluoride (PVDF), a high-performance fluorocarbon resin. This gives the panels their exceptional durability as well as the aesthetic finish.
Using a roll coating process, fluorocarbon coatings are applied to the aluminium coils. The three layers of coatings are dried using baking individual layers at 240°C for nearly 45 seconds. This ensures every layer on the ACP sheets is dry and intact before another layer is applied on top.
Cutting of Panels to Size
When the panels are bonded and coated, Viva ACP panels are then cut into smaller sizes, typically using a CNC router or panel saw, which allows for precise cutting of the panels to the desired size and shape.
The panels are cut into 8×4, 10×4,12×4 ft sizes. We also offer the ultimate facility of customisation in terms of colour, texture and finish. The sheets then get pallet-packaged which protects them during transportation.
Quality Control and Testing
Viva is a strong believer in providing nothing but the best quality Aluminium Composite Panels to our end customers. Our in-house testing facility is equipped with over 60 different testing equipment which tests several aspects of the panels. A range of tests including Tensile Strength, Colour Matching, and Coating Adhesion are carried out to bring exceptionally long-lasting panels. Viva ensures that the final step in the manufacturing process of quality control and testing is up to the bar, and lives up to the customer’s expectations.
Conclusion
Viva ACP lives up to the market reputation by ensuring that all the steps of the manufacturing process are fulfilled with precise accuracy. Leveraging up-to-the-minute technology and industry knowledge, we have introduced a systematic approach to the manufacturing process. By introducing transparency in our production process, we aim to be a partner in India’s & world cladding needs.
You may like : Modern Construction Materials – Aluminium Composite Panel