The story behind the enticing shades of ACP panels: VIVA's Color Coating Lines
VIVA is the only aluminium composite panel manufacturer in India with two colour coating lines that coat aluminium coils of 1000mm, 1220mm, 1250mm, 1500mm, 1550mm, and up to 1670mm. VIVA’s colour coating line works on three-coat two bake technology with the country’s most advanced colour coating line.
A pre-treatment is first done on aluminum coils, followed by chromotherapy. After the process is completed, the coils go in for the first coat of primer. Later, a second coat of paint is applied, and the finished goods are processed.
VIVA uses 70% KYNAR 500 certified PVDF (Fluorinated polyvinyl) paint which conforms to ASTM (American Society for Testing and Materials) and EN (European Nation) standards. KYNAR 500 is a registered trademark of Arkema Inc. Our paints are lead-free.
We also use FEVE (Lumiflon) based paint for exterior application and polyester/PET film for textured surfaces of interior architecture. PVDF has anti-ageing properties, whereas FEVE is used to achieve extraordinary gloss.
We at VIVA can adapt our aluminum composite panel or ACP Sheets to wood, marble, mirror, or any other texture of your choice to suit your architectural needs.
The high-quality coatings of VIVA’s ACP sheets require minimal maintenance, keeping your maintenance costs to a minimum. Both the paints make the ACP board wear-resistant and pollution-proof.
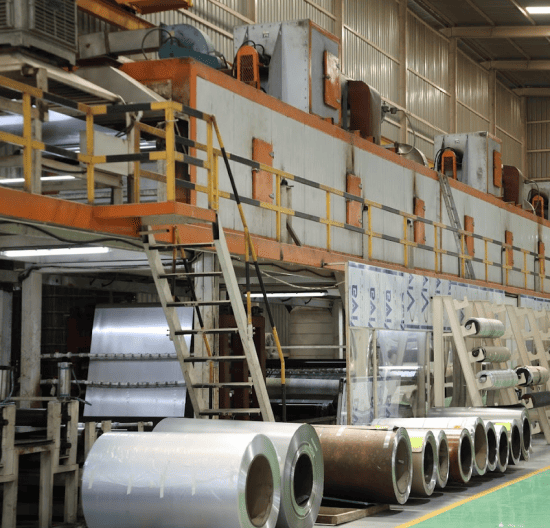
Coating Specifications
PROPERTIES | Test Method | PERFORMANCE |
---|---|---|
Physical Properties of paint | ||
Dry Film Thickness Primer | ASTM D1400 | 5-7 Micron primer coat |
Dry Film Thickness (Top Coat) | ASTM D1400 | 5-7 Micron primer coat |
Specular Glass @ 60° | ASTM D523 | As per Shade |
Colour Difference By Spectrophotometer | ASTM D 2244 | As per Shade |
Scratch Resistance | BS3900 E2 | Max 1KG |
Pencil Hardness | ASTM D3363 | 5-H |
Reverse Impact | ASTM D 2794 | No cracking & No loss of adhesion |
Cupping Test | ECCA T6 | No cracking & No loss of adhesion |
T-bend Test | ASTM D 4145 | 0-2T, No cracking & No loss of adhesion |
Abrasion Test | ASTM D 4060 | Max weight Loss 45 Mg/1000 cycle |
Dry & Wet Adhesion (#) Scratch Test | ASTM D3359 & ASTM D 3359A | 5B |
Chemical Resistance | ||
5% NaOH | ASTM D1308 | No Blistering, De < 5 unit |
5% Hcl | ASTM D1308 | No Blistering, De < 5 unit |
Solvent Resistance | ASTM D 5402 | 100 DR (Double Rub) |
& Other Chemical test also passes as per AAMA 2605 | ||
Long Term testing | ||
Humidity Resistance | ASTM D2247 | Passes 4000 hours |
Salt Spray Resistance / 5% Salt Solution | ASTM B117 | Passes 4000 hours |
Color Retention | ASTM D 523 | Gloss retention Min 60 % up to 4000 Hrs & colour deterioration Maximum 7 unit, Up to 4000 Hrs. |
Gloss Retention | ASTM D2244 | Gloss retention Min 60 % up to 4000 Hrs & colour deterioration Maximum 7 unit, Up to 4000 Hrs. |
QUV Test | ||
Color Retention | ASTM G 154 | Gloss retention Min 60 % up to 4000 Hrs & colour deterioration Maximum 7 unit, Up to 4000 Hrs. |
Gloss Retention | ASTM D4214 | Maximum Rating 8 chalk |
Chalk Resistance | ASTM D4214 | Maximum Rating 8 chalk |
2 Coat Colors
Both of these 2 coat finishes will typically consist of a 5-7 micron primer coat and a 18-20 micron color coat for a nominal dry film thickness of 25(+/-)2 micron
3 Coat Colors
These 3 coat finishes will typically consist of a 5-7 micron primer coat, 18-20 micron color coat and a 5 -7 micron clear coat for a nominal dry film thickness of 35(+/-)2 micron.
Coating Types
Poly Vinylidene Difluoride (PVDF) Coating
A Highly non-reactive thermoplastic fluoropolymer produced by the polymerrization of vinylidene difluoride.
(Warranty 10 years, back to back with KYNAR/HYLAR).
Feve Aluminum Composite Panel Coating
Feve aluminum composite panel is a combination of the advantages of PE coating and PVDF Coating aluminum composite materials. For instance, its glossy and color brightness is the same as for PE coating ACP and its weather resistance is comparable with that of PVDF coating aluminum composite panel.
(Warranty 15 years, back to back with KYNAR/HYLAR).